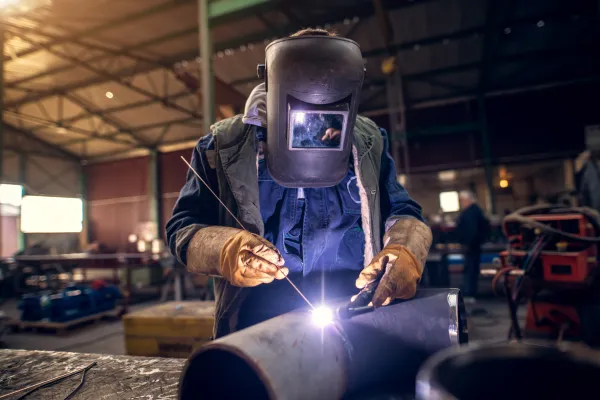
Meistern Sie das Handwerk: Top Wig-Schweißen Techniken enthüllt
WIG-Schweißen: Techniken und Anwendungen
Historische Entwicklung des WIG-Schweißens
Das WIG-Schweißen (Wolfram-Inertgas-Schweißen) hat eine interessante und bedeutende Geschichte. Es entstand in den frühen 1940er Jahren und wurde von Russell Meredith entwickelt, der eine Wolfram-Elektrode und Helium als Schutzgas verwendete. Diese Methode wurde zu einem revolutionären Erfolg, insbesondere während des Zweiten Weltkriegs, als sie hauptsächlich zum Schweißen von Aluminium- und Magnesiumlegierungen in der Luft- und Raumfahrtindustrie eingesetzt wurde (Fractory).
Anwendungsbereiche des WIG-Schweißens
Das WIG-Schweißen bietet viele Vorteile und findet in verschiedenen Industrien breite Anwendung. Aufgrund seiner Präzision und der Möglichkeit, dünne Metalle ohne oder mit minimaler Verwendung von Zusatzwerkstoffen zu schweißen, ist es besonders beliebt bei Anwendungen, die hohe Qualität und Reproduzierbarkeit erfordern.
Schweißen von Dünnmetallen
Das WIG-Schweißen ist weniger aggressiv und daher ideal zum Schweißen von dünnen Metallen. Die präzise Kontrolle der Wärme und die optionale Verwendung von Füllmaterial ermöglichen eine exakte Schweißung ohne Verformung der Materialien (Fractory).
Luft- und Raumfahrtindustrie
Wie bereits erwähnt, spielt das WIG-Schweißen eine zentrale Rolle in der Luft- und Raumfahrtindustrie. Hier wird es verwendet, um dünnwandige Strukturen und kritische Komponenten aus Aluminium- und Magnesiumlegierungen zu verbinden (Fractory).
Automobilindustrie
Auch in der Automobilindustrie wird das WIG-Schweißen eingesetzt, insbesondere bei der Fertigung von Abgasanlagen und Karosserieteilen aus Edelstahl und Aluminium, wo eine hochpräzise Schweißung erforderlich ist.
Weitere Informationen zur Verwendung von WIG-Schweißen in verschiedenen Materialien finden Sie auf unserer Seite WIG-Schweißen Materialien.
Einsatz in der Kunst und im Design
Neben industriellen Anwendungen wird das WIG-Schweißen auch in der Kunst und im Design verwendet, um komplizierte und ästhetisch ansprechende Metallarbeiten zu schaffen.
Die umfassenden Einsatzmöglichkeiten und die hohe Qualität der Schweißnähte machen das WIG-Schweißen zu einer bevorzugten Methode für viele Branchen.
TIG-Schweißen im Detail
TIG-Schweißen, auch als WIG-Schweißen (Wolfram-Inertgasschweißen) bekannt, ist eine präzise Methode des Metallverbindens, die häufig in Unternehmen angewendet wird, die sich für Schweißen interessieren. Diese Sektion behandelt die Funktionsweise und Vorteile des TIG-Schweißens sowie den Einsatz von Füllmaterial.
Funktionsweise des TIG-Schweißens
Beim TIG-Schweißen wird ein Lichtbogen zwischen einer nicht abschmelzenden Wolfram-Elektrode und dem Werkstück erzeugt. Diese Elektrode hat aufgrund ihres hohen Schmelzpunktes und ihrer Langlebigkeit eine zentrale Rolle im Schweißprozess. Der Schweißer verwendet dabei einen Fußpedal oder ein anderes Gerät zur präzisen Steuerung des Stromflusses zum Schweißbad.
Eine Schutzgasatmosphäre aus Argon oder Helium schützt das Schweißbad und die Elektrode vor Oxidation und Verunreinigungen. Diese Technik ermöglicht eine hohe Kontrolle über den Schweißprozess und eignet sich hervorragend für dünne Materialien und Rohre, da sie eine geringe Wärmeeinbringung aufweist und die Mikrostruktur der Metalle erhält.
Vorteile des TIG-Schweißens
TIG-Schweißen bietet zahlreiche Vorteile, die es zu einer bevorzugten Methode in vielen Anwendungen machen:
Hohe Schweißqualität: Das Verfahren erzeugt saubere und präzise Schweißnähte mit minimalem Spritzer, was eine einfache Nachbearbeitung und geringere Polierarbeit erfordert.
Vielseitigkeit: Geeignet für eine Vielzahl von Metallen, einschließlich Edelstahl und Aluminium.
Kontrolle und Präzision: Der Schweißer kann den Schweißstrom sehr genau steuern, was insbesondere bei dünnen Materialien von Vorteil ist.
Optische Qualität: TIG-Schweißen wird oft in Anwendungen verwendet, bei denen das Werkstück nicht beschichtet oder lackiert wird, da die Schweißnähte visuell ansprechend sind.
Weitere Vorteile des WIG-Schweißens finden Sie in unserer Übersicht zu den Vorteilen des WIG-Schweißens.
Verwendung von Füllmaterial beim TIG-Schweißen
Beim TIG-Schweißen kann je nach Projekt ein Füllmaterial verwendet werden, um die Schweißnaht zu verstärken oder zu formen. Der Einsatz von Füllmaterial ist jedoch optional und erfordert zusätzliche Fertigkeiten und Erfahrung, um die richtige Menge und den richtigen Zeitpunkt des Hinzufügens zu bestimmen.
Die Auswahl des richtigen Füllmaterials hängt vom Grundmaterial und den spezifischen Anforderungen der Schweißaufgabe ab. Details zu geeigneten Materialien finden Sie in unserer Materialien-Übersicht für das WIG-Schweißen.
Für eine detaillierte Anleitung zum WIG-Schweißen besuchen Sie bitte unsere Anleitung zum WIG-Schweißen.
Mit diesen Informationen zur Funktionsweise, den Vorteilen und der Verwendung von Füllmaterial beim TIG-Schweißen sind Unternehmen bestens gerüstet, um die vielseitigen Möglichkeiten dieser Schweißtechnik optimal zu nutzen.
TIG-Schweißelektroden
Beim WIG-Schweißen spielen die verwendeten Elektroden eine entscheidende Rolle. Sie unterscheiden sich in Materialzusammensetzung und Eigenschaften, was sich auf ihre Anwendung und Leistung im Schweißprozess auswirkt.
Arten von TIG-Schweißelektroden
Die häufigsten Arten von TIG-Schweißelektroden sind:
Reine Wolframelektroden
Thorierte Wolframelektroden
Lanthanierte Wolframelektroden
Ceriierte Wolframelektroden
Zirconiierte Wolframelektroden
Cer-Lanthan-Elektroden
Diese Elektroden bieten unterschiedliche Vorteile und eignen sich für verschiedene Schweißanforderungen. Eine detaillierte Übersicht dieser Elektroden hilft bei der Auswahl der richtigen Elektrode für den jeweiligen Einsatz.
Eigenschaften und Anwendungen verschiedener TIG-Schweißelektroden
Jede Art von TIG-Schweißelektrode hat spezifische Eigenschaften und Anwendungen:
Reine Wolframelektroden eignen sich besonders für das Schweißen von Aluminium und Magnesium mit Wechselstrom (AC). Sie haben eine hohe Schmelztemperatur und bieten einen stabilen Lichtbogen.
Thorierte Wolframelektroden bestehen aus 1-2% Thorium und sind bevorzugt für Kohlenstoffstahl, Edelstahl und Nickellegierungen. Sie ermöglichen eine höhere Stromtragfähigkeit und eine stabilere Lichtbogenführung (UTI).
Lanthanierte Wolframelektroden enthalten 1-2% Lanthanoxid, was ihre Lebensdauer verlängert und den Lichtbogenstart erleichtert. Sie eignen sich gut für allgemeine Schweißanwendungen.
Ceriierte Wolframelektroden sind mit 1-2% Ceriumoxid angereichert und besonders gut für Niedrigstrom-Anwendungen und präzise Arbeiten geeignet, da sie keine radioaktiven Elemente enthalten.
Zirconiierte Wolframelektroden bieten eine extrem hohe Lichtbogenstabilität und sind besonders widerstandsfähig gegen Verunreinigungen, weshalb sie hauptsächlich für Aluminium und Magnesium geeignet sind.
Cer-Lanthan-Elektroden kombinieren die Vorteile von Cerium und Lanthan, was sie für eine Vielzahl von Anwendungen geeignet macht. Diese Elektroden benötigen weniger Strom und bieten dennoch eine hohe Leistung.
Diese Vielfalt an Elektrodentypen und Eigenschaften ermöglicht es, für jede spezifische Anwendung die optimale Lösung zu finden.
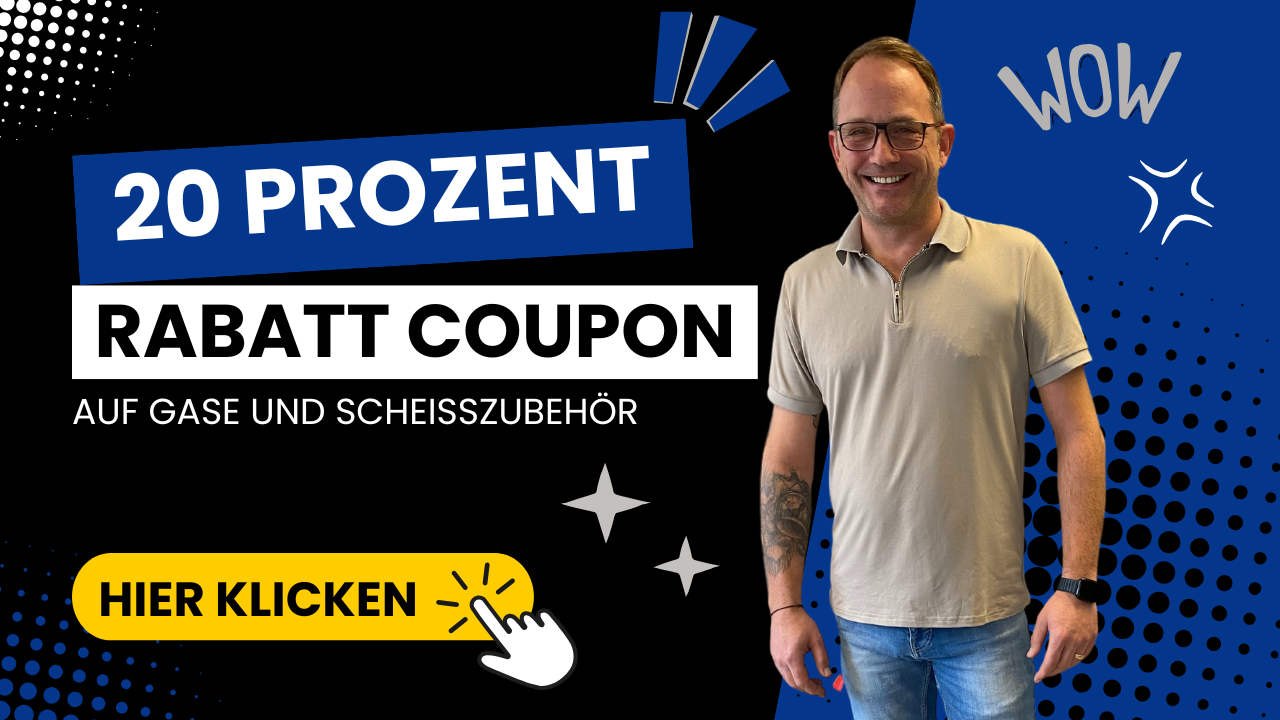
Temperatur beim Schweißen
Einfluss der Temperatur auf die Schweißqualität
Die Temperatur spielt eine entscheidende Rolle im Schweißprozess und beeinflusst die Qualität, Festigkeit und Integrität der Schweißnaht signifikant (Weldero). Ein gründliches Verständnis der Temperaturauswirkungen und die Umsetzung geeigneter Kontrollmaßnahmen können helfen, häufige Schweißfehler zu verhindern, die strukturelle Integrität zu gewährleisten und die Lebensdauer der geschweißten Komponente zu verlängern.
Zu den wichtigsten Temperaturfaktoren gehören:
Schweißtemperatur: Die sorgfältige Kontrolle der Schweißtemperatur ist essenziell, um sicherzustellen, dass die Grundmaterialien und eventuelle Zusatzwerkstoffe korrekt geschmolzen und verbunden werden. Die Schweißtemperatur beeinflusst nicht nur das Schmelzen und Erstarren der Schweißnaht, sondern auch die Mikrostruktur, mechanische Eigenschaften und die allgemeine Qualität der Schweißnaht (Weldero).
Wärmeeinbringung und Abkühlrate: Die Verwaltung der Wärmeeinbringung und der Abkühlrate ist entscheidend, um häufige Schweißdefekte zu verhindern. Eine angemessene Wärme- und Abkühlungsregelung stellt sicher, dass die Schweißnahtfestigkeit optimiert wird und keine Spannungen oder Risse entstehen.
Vorwärmen und Nachwärmen: Vorwärmen vor dem Schweißen und Nachwärmen nach dem Schweißen sind entscheidende Schritte, um die Temperaturkonzentrationen zu kontrollieren und das Risiko von Spannungen und Verformungen zu minimieren.
Bedeutung der Umgebungstemperatur beim Schweißen
Die Umgebungstemperatur, also die Temperatur der Umgebung während des Schweißvorgangs, hat ebenfalls Einfluss auf die Qualität der Schweißnaht. Sowohl hohe als auch niedrige Umgebungstemperaturen können den Schweißprozess und die Eigenschaften der Schweißnaht beeinflussen (Weldero).
Hohe Umgebungstemperatur: Bei hohen Umgebungstemperaturen kann die Kühlrate der Schweißnaht verringert werden, was zu einer groben Mikrostruktur und verminderter Festigkeit führen kann.
Niedrige Umgebungstemperatur: Niedrige Umgebungstemperaturen können eine schnelle Abkühlung bewirken, was Spannungen und Sprödigkeit erhöht. In solchen Fällen ist eine Vorwärmung des Werkstücks oft notwendig.
Die richtige Temperatursteuerung im Schweißprozess trägt wesentlich zur Vermeidung von Schweißfehlern bei. Für detaillierte Anleitungen zum WIG-Schweißen besuchen Sie bitte unsere Seite wig-schweißen anleitung.
Automatisierung im Schweißen
Automatisierung im Schweißen spielt eine entscheidende Rolle in der modernen Fertigungsindustrie. Durch den Einsatz roboterbasierter Systeme können Prozesse effizienter, präziser und konsistenter gestaltet werden.
Roboterische Schweißsysteme
Roboterische Schweißsysteme nutzen fortschrittliche Technologien wie programmierbare Maschinen und Software, um Schweißaufgaben mit minimalem menschlichem Eingriff durchzuführen. Diese Systeme erhöhen die Effizienz und Präzision, indem sie gleichmäßige und wiederholbare Schweißnähte ermöglichen. Zu den wichtigsten Technologien im automatisierten Schweißen gehören:
Roboterarme: Sie führen die eigentlichen Schweißvorgänge aus und können in verschiedene Positionen und Winkel bewegt werden, um genaue Schweißnähte zu erzielen.
Sensoren: Diese überwachen den Schweißprozess in Echtzeit und stellen sicher, dass Parameter wie Temperatur und Abstandsregelung eingehalten werden.
Software: Ermöglicht die Programmierung und Steuerung der Roboter und Sensoren, um spezifische Schweißmuster und -parameter festzulegen.
Vorteile der Automatisierung im Schweißen
Die Automatisierung im Schweißen bietet zahlreiche Vorteile, die besonders für Unternehmen in der Fertigungsindustrie von Bedeutung sind:
Erhöhte Produktivität: Automatisierte Systeme können kontinuierlich arbeiten, wodurch die Produktionskapazität erhöht wird und Engpässe vermieden werden.
Konsistente Qualität: Durch die präzise Steuerung und Wiederholbarkeit automatisierter Systeme wird eine gleichbleibende Schweißqualität gewährleistet.
Kostenreduktion: Reduzierung des Materialabfalls und der Nacharbeit führt zu geringeren Produktionskosten.
Sicherheit: Minimierung des menschlichen Eingriffs reduziert das Risiko für Arbeitsunfälle und Gesundheitsgefahren.

Die zunehmende Nutzung der Automatisierung im Schweißen verändert die Branche grundlegend und führt zu bedeutenden Änderungen bei der Ausführung von Schweißaufgaben und im Management von Arbeitskräften (Weldero).
NDT in der Schweißqualitätskontrolle
Bedeutung der zerstörungsfreien Prüfung (NDT)
Die zerstörungsfreie Prüfung (NDT) spielt eine wesentliche Rolle bei der Sicherstellung der Qualität und Integrität von Schweißnähten in verschiedenen Industrien, einschließlich Bauwesen, Automobil, Luft- und Raumfahrt sowie Energiesektor (Weldero). Fehler in Schweißnähten können zu katastrophalen Ausfällen führen, was erhebliche finanzielle Verluste, Sicherheitsrisiken und potenziellen Verlust von Menschenleben bedeutet. Daher ist die gründliche Inspektion von Schweißnähten von entscheidender Bedeutung.
NDT bietet eine zuverlässige und nicht-invasive Methode zur Erkennung von Defekten, die die Integrität einer Struktur gefährden könnten. Dadurch trägt NDT zur Lebensverlängerung von Komponenten und zur Erhöhung der Sicherheit verschiedener Industrien bei (Weldero).
NDT-Methoden für die Schweißqualitätskontrolle
Es gibt verschiedene NDT-Methoden, die eingesetzt werden, um sicherzustellen, dass Schweißnähte den erforderlichen Standards und Spezifikationen entsprechen, ohne die geschweißten Komponenten zu beschädigen (Weldero). Zu den wichtigsten Methoden gehören:
Visuelle Inspektion (VT): Dabei handelt es sich um die einfachste Form der NDT, bei der Schweißnähte mit bloßem Auge oder mit Hilfsmitteln wie Lupen oder Endoskopen untersucht werden.
Radiografische Prüfung (RT): Verwendet Röntgenstrahlen oder Gammastrahlen zur Erkennung von internen Defekten in Schweißnähten.
Ultraschallprüfung (UT): Nutzt hochfrequente Schallwellen, um Fehler in Schweißnähten zu erkennen und die Materialdicke zu messen.
Magnetpulverprüfung (MT): Verwendet magnetische Felder und feine Partikel zur Erkennung von Oberflächen- und unterirdischen Rissen in ferromagnetischen Materialien.
Eindringprüfung (PT): Nutzt fluoreszierende oder farbige Flüssigkeiten, die auf die Oberfläche der Schweißnaht aufgetragen werden, um Oberflächenfehler zu erkennen.
Wirbelstromprüfung (ET): Verwendet elektromagnetische Induktion zur Erkennung von Oberflächen- und nahe Oberflächenfehlern in leitfähigen Materialien.
Schallemissionsprüfung (AE): Nutzt akustische Emissionen, um dynamische Prozesse wie Rissbildung oder Kunststoffverformung in Echtzeit zu überwachen.
Durch den Einsatz dieser Methoden tragen Unternehmen zur Vermeidung von Fehlern, zur Verlängerung der Nutzungsdauer von Bauteilen und zur Erhöhung der Sicherheit bei (Weldero).