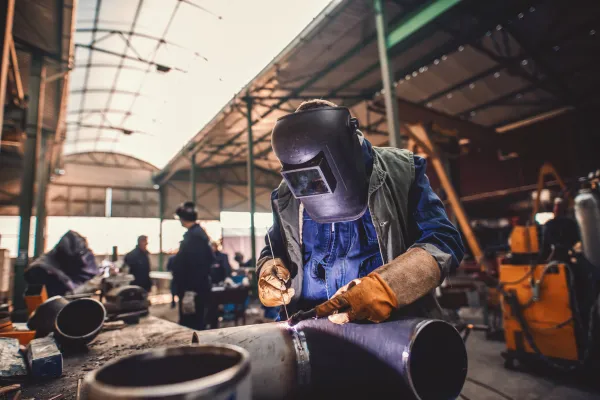
Meisterhaft schweißen: Die besten WIG-Schweißen Materialien
WIG-Schweißen Grundlagen
Gas Tungsten Arc Welding (GTAW)
Das Gas Tungsten Arc Welding (GTAW), auch bekannt als Tungsten Inert Gas (TIG) Schweißen, ist ein Verfahren, das eine nicht verbrauchbare Wolframelektrode und ein inertes Schutzgas verwendet, um das Schweißgebiet und die Elektrode vor Oxidation oder Verschmutzung zu schützen. Abhängig vom zu schweißenden Material kann ein Zusatzwerkstoff verwendet werden oder auch nicht (Wikipedia).
GTAW wird häufig in folgenden Branchen eingesetzt:
Luft- und Raumfahrt: Kritische Anwendungen wie die Fertigung von Raumfahrzeugen erfordern präzise, widerstandsfähige Schweißnähte.
Fahrradindustrie: Besonders geeignet für kleine Durchmesserrohre.
Rohrleitungsbau: Ideal für Wurzelschweißungen und Wartungsarbeiten (Wikipedia).
Ausrüstung und Materialien
Für den erfolgreichen Einsatz des WIG-Schweißens werden spezielle Ausrüstungen und Materialien benötigt. Dazu gehören:
Schweißbrenner: Enthält eine nicht verbrauchbare Wolframelektrode.
Schweißstromquelle: Eine konstantstrombetriebene Stromquelle ist notwendig, um die notwendige Stabilität zu gewährleisten.
Schutzgasquelle: Verwendung von inerten Gasen wie Argon oder Helium, um das Schweißbad vor Umwelteinflüssen zu schützen (Wikipedia).
Tabellenübersicht: Welches Material für welches Verfahren?
Diese Tabelle bietet eine schnelle Übersicht über die häufigsten Materialien und die dazugehörigen Gas- und Zusatzwerkstoffempfehlungen.
TIG-Schweißgeräte sind speziell an die Anforderungen des Verfahrens angepasst. Wichtige Überlegungen bei der Auswahl des richtigen Geräts beinhalten:
Wolframelektrode: Die Wahl der Elektrode hängt stark vom Schweißmaterial ab. Es gibt verschiedene Arten von Wolframelektroden wie reines Wolfram, Thorium-, Lanthan- und Zirkonoxid-haltige Elektroden.
Schutzgasregler: Ein hochwertiger Regler ist notwendig, um den Gasfluss präzise zu steuern. Informieren Sie sich über spezifische wig-schweißen gas.
Stromquelle: Konventionelle oder inverterbasierte Stromquellen, je nach Bedarf und Präferenz (Wikipedia).
Anwendungen von WIG-Schweißen
Industrieanwendungen
Das WIG-Schweißen, auch bekannt als Gas Tungsten Arc Welding (GTAW), findet breite Anwendung in verschiedenen Industriezweigen. Aufgrund seiner Präzision und hohen Qualität ist es eine bevorzugte Methode für Anwendungen, die höchste Schweißnahtqualität erfordern, z.B. im Maschinenbau und in der Fertigung von Fahrradrahmen. WIG-Schweißen eignet sich besonders gut für Materialien wie Edelstahl, Aluminium und Titan. Weitere Einzelheiten zu den Vorteilen dieser Technik finden Sie in unserem Artikel über wig-schweißen vorteile.
Luft- und Raumfahrtindustrie
In der Luft- und Raumfahrtindustrie ist das WIG-Schweißen unverzichtbar. Die Methode wird bei der Herstellung von Flugzeugen und Raumfahrzeugen verwendet, da sie präzise und saubere Schweißnähte bietet, die den extrem hohen Anforderungen der Branche gerecht werden. Die Fähigkeit des WIG-Schweißens, mit dünnen Materialien zu arbeiten, ist besonders wichtig für die Leichtbauweise, die in der Luft- und Raumfahrt von entscheidender Bedeutung ist. Weitere Anwendungsmöglichkeiten in dieser Branche werden in unserem Abschnitt über wig-schweißen techniken erläutert.
Rohrschweißen in der Herstellung
Im Bereich der Rohrschweißung ist das WIG-Schweißen eine bevorzugte Technik, insbesondere für Wurzelschweißungen und dünnwandige Rohre. Diese Methode ermöglicht es, starke und dichte Schweißnähte zu erzeugen, die notwendig sind, um Leckagen zu verhindern und die strukturelle Integrität zu gewährleisten. Diese Technik wird in der Fertigung von Anlagen und Rohrleitungssystemen, auch in der Lebensmittel- und Pharmaindustrie, häufig eingesetzt. Hinweise zur sicheren Anwendung finden sich in unserer wig-schweißen anleitung.
Das WIG-Schweißen hat sich in diesen Anwendungen aufgrund seiner Vielseitigkeit und hohen Qualität bewährt.
Vorteile von WIG-Schweißen
Präzision und Qualität der Schweißnähte
WIG-Schweißen, auch als Gas Tungsten Arc Welding (GTAW) bekannt, bietet eine herausragende Präzision und Qualität der Schweißnähte. Mit dieser Methode können feinste und sauberste Schweißnähte erzeugt werden, was besonders bei sensiblen Anwendungen wie in der Luft- und Raumfahrtindustrie von Vorteil ist (Wikipedia). Dies ermöglicht eine exakte Kontrolle über den Schweißprozess und führt zu minimalem Verzug und einer hohen Ästhetik der Nähte.
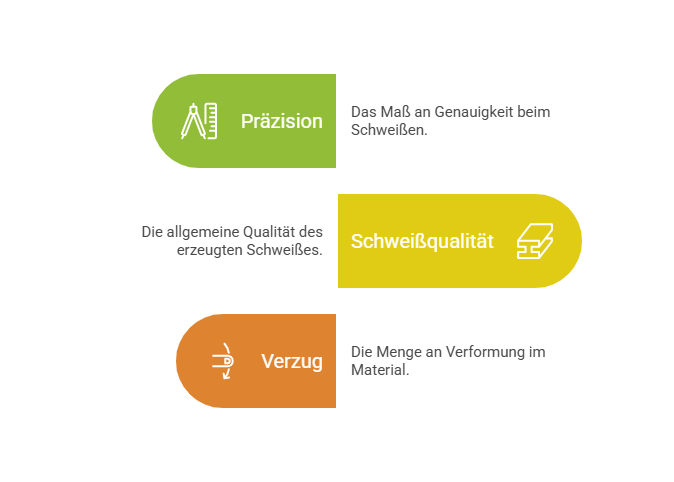
Widerstandsfähige Schweißnähte
Ein weiterer Vorteil des WIG-Schweißens ist die Widerstandsfähigkeit der Schweißnähte. Diese Methode erzeugt besonders robuste Verbindungen, die selbst unter extremen Bedingungen standhalten. Dies macht sie ideal für kritische Anwendungen wie das Verschließen von Atommüllbehältern und Reparaturarbeiten in der Industrie (Wikipedia). Die Schweißnähte sind beständig gegen Korrosion und bieten eine ausgezeichnete mechanische Festigkeit.
Anwendbarkeit in verschiedenen Branchen
Das WIG-Schweißen ist in einer Vielzahl von Branchen anwendbar, darunter die Luft- und Raumfahrt, die Fertigungsindustrie und die Rohrschweißung. Es wird häufig für die Herstellung von Raumfahrzeugen, kleinen Rohrleitungen in der Fahrradindustrie und für Wurzelnähte an Rohren verwendet (Wikipedia). Auch in der Wartung und Reparatur ist diese Methode äußerst nützlich, da sie es ermöglicht, präzise und langlebige Schweißnähte zu erzeugen.
WIG-Schweißen vs. Laser-Schweißen
Prozessvergleich
Der Prozess des WIG-Schweißens (Wolfram-Inertgasschweißen) und Laser-Schweißens unterscheidet sich grundlegend in verschiedenen Aspekten.
WIG-Schweißen nutzt eine nicht-schmelzende Wolframelektrode und ein Inertgas (zum Beispiel Argon) zum Schutz des Schweißbereichs. Der Einsatz von Inertgas minimiert Oxidation und Verunreinigungen. Laser-Schweißen hingegen verwendet einen konzentrierten Laserstrahl, um Materialien präzise und schnell zu schmelzen und zu verbinden.
Beide Methoden haben ihre spezifischen Stärken und Schwächen, je nach Anwendung und Anforderungen.
Materialien und Anwendungen
Die Wahl der geeigneten Schweißtechnik hängt von den zu verarbeitenden Materialien und den spezifischen Anwendungen ab.
WIG-Schweißen: WIG-Schweißen wird häufig für Materialien wie Edelstahl, Aluminium, Kupfer und Titan verwendet. Es zeichnet sich durch seine hohe Präzision und die Qualität der Schweißnähte aus, was es ideal für Anwendungen in der Luft- und Raumfahrtindustrie, der Rohrleitungsherstellung und für medizinische Geräte macht. Weitere Details über die Vorteile und Techniken des WIG-Schweißens finden Sie in unseren Artikeln wig-schweißen techniken und wig-schweißen vorteile.
Laser-Schweißen: Laser-Schweißen ist bekannt für seine Geschwindigkeit und Präzision. Es wird für verschiedene Materialien wie Aluminium, Titan, Kohlenstoffstähle, HSLA-Stähle und Edelstahl eingesetzt. In der Automobilindustrie wird es zum Beispiel für den Zusammenbau von Karosserieelementen und tragenden Komponenten verwendet. Weitere industrielle Anwendungen umfassen das Schweißen elektronischer Bauteile und Stahlkonstruktionen (Hairful).
Insgesamt können beide Techniken in verschiedenen Branchen eingesetzt werden, wobei die Wahl des geeigneten Verfahrens von den spezifischen Anforderungen und den zu verarbeitenden Materialien abhängt.
Herausforderungen beim WIG-Schweißen
Das WIG-Schweißen (Wolfram-Inertgasschweißen) bietet viele Vorteile, aber es gibt auch einige Herausforderungen, die überwunden werden müssen, um optimale Schweißergebnisse zu erzielen.
Schweißfehler und Lösungen
Beim WIG-Schweißen können verschiedene Schweißfehler auftreten. Dazu gehören Risse, Porosität und mangelnde Durchdringung. Diese Fehler können durch eine sorgfältige Auswahl der wig-schweißen materialien und die richtige Technik minimiert werden.
Einige übliche Schweißfehler und deren Lösungen:
Gasflusskontrolle und -muster
Die Kontrolle des Gasflusses und -musters ist entscheidend für die Qualität der Schweißnähte. Ein konstanter und gleichmäßiger Gasfluss verhindert Oxidation und verbessert die Schweißqualität. Helium-Schirmgas ist besonders wichtig, da es hilft, die Schmelzzone vollständig zu durchdringen.
Für eine effektive Gasflusskontrolle sollten Sie:
Den Gasfluss korrekt einstellen
Sicherstellen, dass die Gasdüse sauber und frei von Verstopfungen ist
Die Umgebungsluftbewegung minimieren, um die Gasabschirmung zu gewährleisten
Qualitäts- und Reproduzierbarkeitsprobleme
Ein weiteres häufiges Problem beim WIG-Schweißen sind Qualitäts- und Reproduzierbarkeitsprobleme. Die Konsistenz der Schweißnähte kann durch verschiedene Faktoren beeinflusst werden. Dazu gehören Schwankungen in der Stromstärke, unterschiedliche Materialdicken und -typen sowie die manuelle Fertigkeit des Schweißers.
Um diese Probleme zu minimieren, sollten Schweißer:
Regelmäßig die Geräte warten und kalibrieren
Einheitliche Arbeitsprozesse entwickeln
Hochwertige wig-schweißen techniken anwenden
Eine konsistente Qualitätskontrolle ist unerlässlich, um die Reproduzierbarkeit der Schweißnähte zu gewährleisten. Dies beinhaltet regelmäßige Inspektionen und Tests der Schweißnähte nach festgelegten Standards.
Durch die Bewältigung dieser Herausforderungen kann WIG-Schweißen effektiver und zuverlässiger durchgeführt werden, was zu langlebigen und hochwertigen Schweißverbindungen führt.
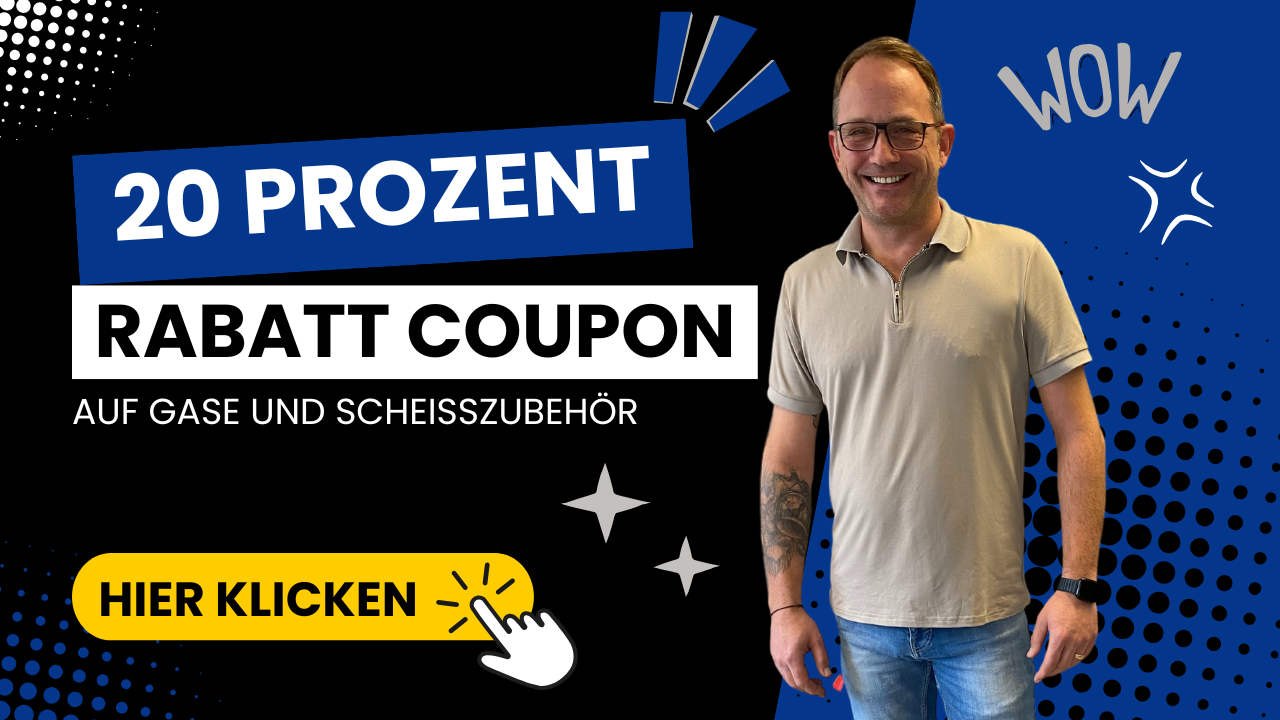
Zukünftige Entwicklungen im WIG-Schweißen
Laser-Schweißen mit Drahtvorschub
Das Laser-Schweißen mit Drahtvorschub gewinnt zunehmend an Bedeutung und wird weltweit aktiv erforscht. Insbesondere Hochleistungslaser bei einer Wellenlänge von etwa 1000 nm ersetzen konventionelle CO2-Laser in verschiedenen Anwendungen. Diese Hochleistungslaser bieten Vorteile wie die Strahlführung über optische Fasern. Bei diesem Schweißprozess sind typische Probleme wie Durchschmelzfehler, Schweißraupenporosität und Inkonsistenzen in der Schweißqualität und -reproduzierbarkeit weit verbreitet (Handbook of laser welding technologies).
Optimierung von Schweißprozessen
Die Optimierung von Schweißprozessen zielt darauf ab, die Effizienz und Qualität der Schweißnähte zu verbessern. Technologische Fortschritte wie automatisierte Überwachungssysteme und präzisere Steuerungen helfen dabei, Variabilitäten zu reduzieren und die Reproduzierbarkeit zu erhöhen. Diese Optimierungen sind für Branchen wie die Automobilindustrie von besonderem Interesse, wo das Laser-Schweißen für das Verbinden von Dünnblechelementen sowie tragenden Komponenten wie Rahmen und Streben eingesetzt wird (Handbook of laser welding technologies).
Verbesserung der Schweißqualität und Effizienz
Die Verbesserung der Schweißqualität und Effizienz ist ein kontinuierlicher Prozess. Moderne Technologien nutzen hierbei Methoden wie die Temperaturregelung und den Einsatz von Schutzgasen. Durch eine verbesserte Gasflusskontrolle und -muster können Schweißfehler minimiert werden. Weitere Entwicklungen umfassen die Optimierung der Geräteausstattung und den Einsatz fortschrittlicher Werkstoffe, um die Langlebigkeit und Widerstandsfähigkeit der Schweißnähte zu erhöhen.