
Der Weg zum Perfekten Schweißnähten: Wig-Schweißen Gas Vorgestellt
Das Wesentliche des WIG-Schweißens
Prozessübersicht des WIG-Schweißens
WIG-Schweißen, auch bekannt als Wolfram-Inertgas-Schweißen, ermöglicht erstklassige Schweißnähte durch das Brennen eines Lichtbogens zwischen einer temperaturbeständigen, nicht schmelzenden Wolframelektrode und dem Werkstück. Dieser Prozess verwendet ein inertes Schutzgas, das um die Elektrode zirkuliert und den Lichtbogen schützt. Dadurch werden Verunreinigungen und Oxidationen vermieden, was zu einer hohen Schweißqualität führt.
Die am häufigsten verwendete Gasart für das WIG-Schweißen ist Argon, da es sich leicht ionisiert und den Schweißprozess vereinfacht. Auch ein Hochfrequenzstart wird oft eingesetzt, um den Lichtbogen zu zünden, was den Prozess noch effizienter gestaltet. Weitere Details zur Technik finden Sie in unserem Artikel über wig-schweißen techniken.
Verwendung von WIG-Schweißen
WIG-Schweißen wird in vielen Bereichen eingesetzt, von der Luft- und Raumfahrt bis hin zu feinmechanischen Arbeiten. Diese Schweißmethode ist besonders geeignet für die Verarbeitung unterschiedlicher Metalle und Legierungen wie Stahl, Edelstahl, Kupfer, Titan und Nickel. Dadurch erhalten Schweißarbeiten eine hohe Präzision und Zuverlässigkeit.
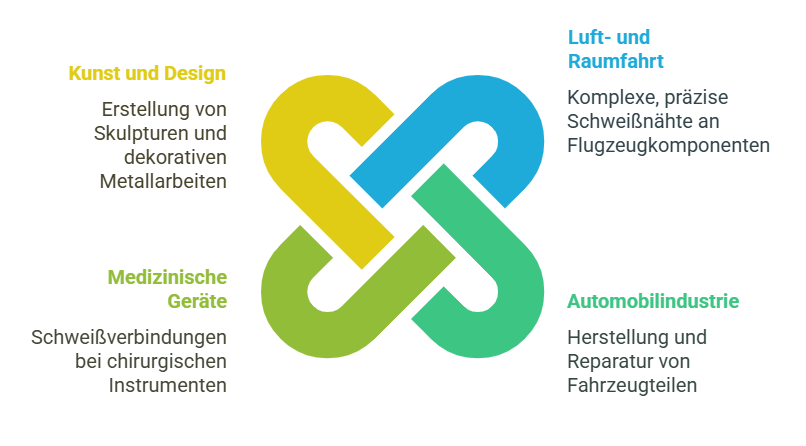
Die hohe Qualität der Schweißnähte macht das WIG-Schweißen ideal für Anwendungen, bei denen perfekte und saubere Ergebnisse unerlässlich sind. Weitere Informationen zu den Vorteilen dieser Schweißmethode finden Sie in unserem Beitrag über wig-schweißen vorteile sowie eine detaillierte Anleitung in wig-schweißen anleitung.
Im Wesentlichen bietet das WIG-Schweißen durch die Kombination aus präziser Technik und flexiblen Anwendungsmöglichkeiten eine hervorragende Lösung für zahlreiche Metallverarbeitungsanforderungen. Entdecken Sie auch mehr über die verwendeten Materialien unter wig-schweißen materialien.
Vorteile und Anwendungen von WIG-Schweißen
WIG-Schweißen, auch bekannt als Wolfram-Inertgas-Schweißen, bietet zahlreiche Vorteile gegenüber anderen Schweißmethoden. Im Folgenden werden die Qualität der Schweißnähte sowie die verschiedenen Anwendungsgebiete näher beleuchtet.
Qualität der Schweißnähte
Die Qualität der WIG-Schweißnähte ist bemerkenswert. Dieser Schweißprozess ermöglicht es, sowohl mit als auch ohne Zusatzwerkstoff zu arbeiten, was zu sauberen und spritzerfreien Nähten führt (Source). Dies wird durch die präzise Kontrolle der Wärmeeinbringung und die hohe Stabilität des Lichtbogens erreicht.
Diese Eigenschaften machen WIG-Schweißen besonders attraktiv für Anwendungen, bei denen hohe Nahtqualität und Ästhetik wichtig sind, wie beispielsweise im Flugzeugbau und der Medizintechnik.
Anwendungsgebiete des WIG-Schweißens
WIG-Schweißen wird in vielen verschiedenen Branchen und für verschiedene Materialien eingesetzt. Hier sind einige der häufigsten Anwendungsgebiete:
Industrie und Fertigung: WIG-Schweißen wird häufig für die Fertigung von industriellen Anlagenteilen und Maschinen verwendet, wo Präzision und Langlebigkeit entscheidend sind.
Luft- und Raumfahrt: Die hohe Qualität und Stabilität der Schweißnähte machen WIG-Schweißen zu einer bevorzugten Methode im Flugzeugbau.
Medizintechnik: Die sauberen und korrosionsbeständigen Schweißnähte sind ideal für die Herstellung von medizinischen Geräten und Instrumenten.
Automobilindustrie: In der Automobilindustrie wird WIG-Schweißen verwendet, um leichte und starke Verbindungen an Fahrzeugkomponenten zu erstellen.
Durch die präzise Kontrolle der Temperatur und die Möglichkeit, mit verschiedenen Gasen wie Argon zu arbeiten, das die Zündung erleichtert (EWM Group), ist WIG-Schweißen eine vielseitige und zuverlässige Methode.
Elektroden und Schutzgas beim WIG-Schweißen
Verwendung von Wolframelektroden
Wolframelektroden sind ein zentrales Element im WIG-Schweißprozess. Sie bieten eine hervorragende elektrische Leitfähigkeit und schützen den Lichtbogen sowie das Schweißbad vor Verunreinigungen durch Inertgas.
Wolframelektroden gibt es in verschiedenen Ausführungen, wie reine Wolframelektroden, thorierte Wolframelektroden oder zirconiierte Wolframelektroden. Jede Variante hat spezielle Eigenschaften, die je nach Anwendung und Material ausgewählt werden können.
Bedeutung von Schutzgasen
Schutzgase spielen eine entscheidende Rolle im WIG-Schweißprozess. Sie gewährleisten, dass die Schweißnaht frei von Verunreinigungen bleibt, indem sie den Lichtbogen und das Schweißbad vor Umwelteinflüssen schützen.
Das am häufigsten verwendete Schutzgas beim WIG-Schweißen ist Argon. Argon erleichtert die Zündung, da es sich leichter ionisiert als andere Gase und somit den Schweißprozess vereinfacht.
Schutzgase wie Argon, Helium oder deren Mischungen werden je nach den Anforderungen des zu schweißenden Materials und des spezifischen Schweißprozesses ausgewählt. Während Argon allein oft für Standardanwendungen verwendet wird, bieten Helium und Mischungen eine höhere Lichtbogenenergie und ermöglichen schnelleres Schweißen.
Indem man die richtigen Elektroden und Schutzgase auswählt, kann man die Qualität und Effizienz des WIG-Schweißprozesses erheblich verbessern. Schweißer können durch die Kombination verschiedener Gase und Elektrodenarten maßgeschneiderte Lösungen für ihre spezifischen Anforderungen entwickeln und dabei stets die bestmögliche Schweißnahtqualität erzielen.
Temperaturkontrolle beim WIG-Schweißen
Die Temperaturkontrolle spielt eine entscheidende Rolle beim WIG-Schweißen, da hohe Betriebstemperaturen erreicht werden und die Auswirkungen dieser Temperaturen auf das Schweißmaterial erheblich sein können.
Hohe Betriebstemperaturen
Das WIG-Schweißen (Wolfram-Inertgas-Schweißen) arbeitet bei extrem hohen Temperaturen. Temperaturen im Schweißkegel können bis zu 4800°C erreichen (AXXAIR). Diese Temperaturen ermöglichen eine einfache Umwandlung von Elektrizität in Wärme, wodurch das Schweißgut ohne direkten Kontakt fusioniert und verbunden wird.
Die Verwendung von Argon als Schutzgas erleichtert das Zünden, da es im Vergleich zu anderen Gasen leichter ionisiert (EWM Group). Bei Betriebstemperaturen über 6000 Grad Fahrenheit sorgen diese Bedingungen für eine effektive und präzise Schweißung.
Auswirkungen der Temperaturen
Hohe Temperaturen können verschiedene Auswirkungen auf das Schweißmaterial haben. Einerseits gewährleisten sie eine vollständige Verschmelzung der Werkstücke, andererseits können sie jedoch potenziell negative Auswirkungen wie Verzug oder Spannungsrisse verursachen. Um dieser Problematik entgegenzuwirken, ist eine präzise Temperaturkontrolle unerlässlich.
Ein Beispiel für die effektive Temperaturkontrolle ist der Hochfrequenzstart beim WIG-Schweißen, der stets als ein Stromimpuls mit sehr hoher Spannung erfolgt. Diese Spannungsspitzen sind jedoch auf maximal 15 kV für manuell betriebene Schweißbrenner begrenzt, um die Sicherheit zu gewährleisten.
Um die Qualität der Schweißnaht und die Sicherheit zu erhöhen, sollten stets Schutzmaßnahmen ergriffen werden. Dies umfasst das Tragen von Schutzausrüstung wie trockene Lederhandschuhe, Schutzkleidung und die Verwendung von Isoliermatten.
Gesundheitsrisiken und Sicherheitsmaßnahmen beim WIG-Schweißen
Beim WIG-Schweißen gibt es verschiedene Gesundheitsrisiken, die nicht unterschätzt werden dürfen. Diese Risiken können durch entsprechende Sicherheitsmaßnahmen und Schutzausrüstung minimiert werden.
Gefahrenquellen beim WIG-Schweißen
WIG-Schweißen erzeugt verschiedene gesundheitsschädliche Gase und Strahlungen. Hier sind einige der wichtigsten Gefahrenquellen:
Stickstoffoxide (NOx) und Ozon: WIG-Schweißen erzeugt Stickstoffoxide und Ozon, besonders durch die UV-Strahlung des Lichtbogens. Dies ist besonders bei Aluminium-Silizium-Legierungen und reinem Aluminium der Fall.
Radioaktive Strahlung: Die Verwendung von thoriumoxidhaltigen Wolframelektroden kann zu radioaktiver Belastung durch Einatmen von Rauch führen. Besonders beim Schweißen von Aluminium-Materialien ist dies ein Risiko. Der Belastungsgrad hängt vom Schweißverfahren ab und ist bei Gleichstromschweißen (DC) geringer als bei Wechselstromschweißen (AC).
Nickeloxid und Chrom(VI)-Verbindungen: Beim Schweißen von Chrom-Nickel-Stahl entstehen Nickeloxid und Chrom(VI)-Verbindungen, die krebserregend sind und das Atemwegssystem sowie das Nervensystem schädigen können.
Präventive Maßnahmen und Schutzausrüstung
Um die Gesundheitsrisiken beim wig-schweißen gas zu reduzieren, sollten folgende präventive Maßnahmen und Schutzausrüstungen eingesetzt werden:
Punktabsaugung: Die effektive Absaugung von Schweißrauch und Ozon direkt an der Entstehungsstelle ist essenziell. Hallenbelüftungssysteme sollten implementiert werden, um die Ausbreitung von Ozon zu verhindern.
Alternative Elektroden: Anstelle von thoriumoxidhaltigen Wolframelektroden sollten alternative Zusätze wie Cerium oder Lanthan verwendet werden.
Schutzausrüstung: Die Verwendung von Schutzkleidung, ordnungsgemäßer Isolierung, trockenen Lederhandschuhen, ausreichendem Abstand und Isoliermatten ist unerlässlich, besonders beim Umgang mit der Hochfrequenzzündung (EWM Group).
Durch das Einhalten dieser Sicherheitsmaßnahmen können die Risiken beim WIG-Schweißen erheblich reduziert werden.
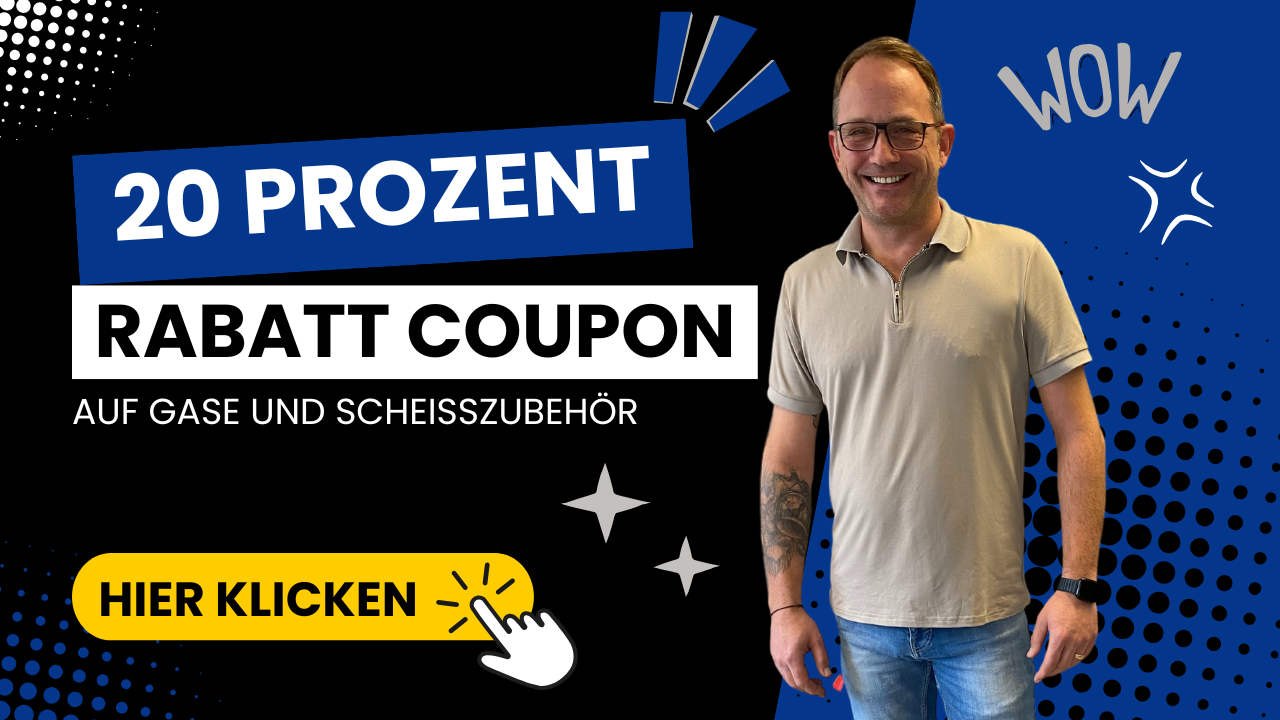
Vergleich mit anderen Schweißmethoden
Das WIG-Schweißen unterscheidet sich deutlich von anderen Schweißmethoden wie dem MIG-Schweißen und dem MAG-Schweißen. Im Folgenden werden die Unterschiede und Anwendungsbereiche der verschiedenen Schweißverfahren erläutert.
Unterschiede zum MIG-Schweißen
Das WIG-Schweißen (Wolfram-Inert-Gas) und das MIG-Schweißen (Metall-Inert-Gas) nutzen unterschiedliche Techniken und Gase.
Beim WIG-Schweißen kommt eine nicht abschmelzende Wolframelektrode zum Einsatz, während beim MIG-Schweißen ein Schmelzdräht verwendet wird. Das Schutzgas beim WIG-Schweißen besteht aus Inerten Gasen wie Argon oder Helium, die den Schweißbereich vor Oxidation schützen und die Lichtbogenstabilität gewährleisten (Fronius).
Anwendungsgebiete von MIG- und MAG-Schweißen
MIG- und MAG-Schweißen sind zwei Varianten des Metallschutzgasschweißens. Während das MIG-Schweißen Inertgase wie Argon und Helium verwendet, um den Schweißbereich zu schützen, nutzt das MAG-Schweißen aktive Schutzgase wie Kohlendioxid (CO2) oder Sauerstoff (O2) zusätzlich zum Trägergas Argon (Fronius).
Das MIG-Schweißen ist besonders geeignet für Nichteisenmetalle wie Aluminium, Magnesium, Kupfer und Titan, während das MAG-Schweißen häufig für das Schweißen von unlegierten, niedriglegierten und hochlegierten Stählen verwendet wird.